Engineering
RAPID MELTING ENERGY SAVING ALUMINIUM MELTING FURNACE (ER Model)
The central melting furnace is designed to handle large quantities of metal, offering high melting capacities to meet the production demands of the facility. It provides a controlled environment for the melting process, ensuring that the metal reaches the desired temperature and consistency for downstream operations.
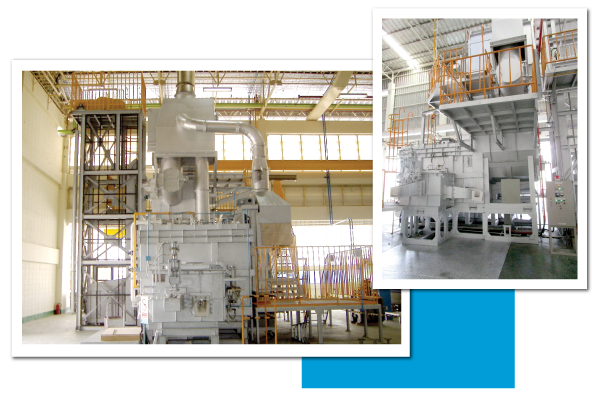
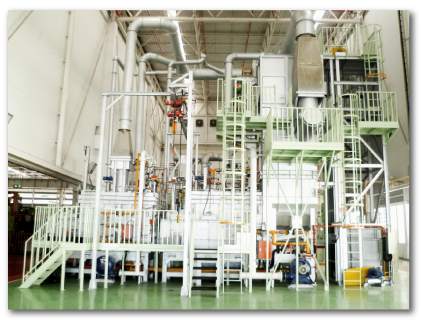
SPECIFICATIONS
1. Gas: Town/City gas, Natural gas, Propane, Butane
2. Oil: Heavy oil grade, Diesel oil, Kerosene, etc.
3. Melting rate 500 - 2,500 kg
4. Holding rate 1,500-6,500 kg
ER Furnace Specification
Type | Melting Rate (Kg/Hr) |
Holding Capacity (Kg) |
Melt. Burner Cap. (Kcal/Hr) |
Hold. Burner Cap. (Kcal/Hr) |
---|---|---|---|---|
ER-500 | 500 | 1,500 | 400,000 | 200,000 |
ER-700 | 700 | 2,000 | 500,000 | 300,000 |
ER-1000 | 1,000 | 3,000 | 600,000 | 400,000 |
ER-1500 | 1,500 | 4,000 | 900,000 | 400,000 |
ER-2000 | 2,000 | 5,000 | 1,200,000 | 500,000 |
ER-2500 | 2,500 | 6,000 | 1,500,000 | 600,000 |