Engineering
ALUMINIUM MELTING AND HOLDING FURNACE (LCM Model)
The beginning of LCM furnace "We have been supplying aluminum melting furnaces to the die-casting industry for decades, consistently striving to meet our customers' evolving needs. Through extensive research, we have identified the key factors that are crucial for an optimal melting furnace. Based on our findings, we have compiled the following essential requirements.".
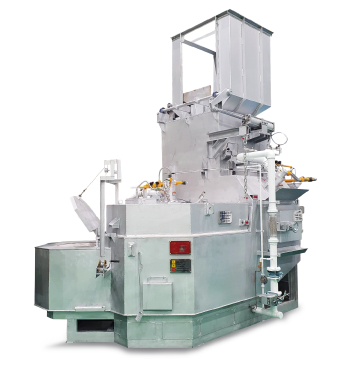
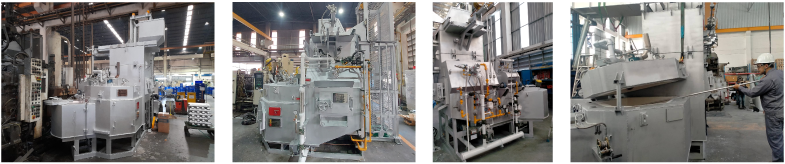
1. Fuel Efficiency Enhancement:
- By designing a smaller holding room space, we can achieve rapid temperature rises.
- Minimizing the intrusion of outside air into the holding room to prevent excessive cooling of the molten metal.
- Utilizing a combustion burner directly for material melting to expedite the melting process.
- Implementing intermittent control of the burner combustion, preventing wasteful combustion through regular ON-OFF cycles based on material input frequency.
2. Prevention of Outside Air Intrusion:
- Preventing the ingress of outside air into the holding room to suppress molten metal oxidation.
- Transitioning from direct heating to indirect heating methods (indirect heating involves directing the burner flame away from the molten metal) to mitigate oxidation.
- Employing intermittent melting burner control to minimize aluminum oxidation during the melting process.
3. Enhanced Maintainability:
- Designing a holding room with reduced height to facilitate cleaning of blind spots within the furnace.
- Enhancing maintainability by relocating devices to lower positions, making them easily accessible for cleansing.
4. Extended lifespan:
- Selecting reliable burners exclusively made in Japan, ensuring suitability for indirect heating of molten metal and fast melting speed.
- In-house production with rigorous quality management practices to ensure stable and flawless manufacturing.
- Providing comprehensive after-sales support to customers, ensuring their needs are addressed even after delivery.
FROM CONVENTIONAL FURNACE TO LCM FURNACE
Main qualification is that the ceilling wall of Holding room is Lower and it becomes very compact
Comparative Information | LCM-150 | SER-150 |
---|---|---|
Total Aluminium Melting | 600 kg | 600 kg |
Total Gas Comsumption | 11.7 m3 | 14 m3 |
Diff | 2.3 m3 | |
% Diff | 16.40% |
SPECIFICATIONS
1. Fuels : Gas (Melting and Holding)
2. Melting rate 150-700 kg
3. Holding rate 600-2,000 kg
LCM Furnace Specification
Type | Melting Rate (Kg/Hr) |
Holding Capacity (Kg) |
Melt. Burner Cap. (Kcal/Hr) |
Hold. Burner Cap. (Kcal/Hr) |
---|---|---|---|---|
LCM-100 | 100 | up to 450 | 80,000 | 50,000 |
LCM-150 | 150 | up to 550 | 80,000 | 50,000 |
LCM-200 | 200 | up to 700 | 120,000 | 50,000 |
LCM-250 | 250 | up to 900 | 150,000 | 100,000 |
LCM-300 | 300 | up to 1,100 | 150,000 | 100,000 |
LCM-400 | 400 | up to 1,300 | 200,000 | 100,000 |
LCM-500 | 500 | up to 1,500 | 350,000 | 200,000 |
LCM-600 | 600 | up to 2,000 | 400,000 | 200,000 |
LCM-700 | 700 | up to 2,500 | 400,000 | 200,000 |